AI-Powered Predictive Maintenance: Transforming Industry Efficiency and Equipment Lifespan
AI for Predictive Maintenance: Revolutionizing Manufacturing and Beyond
Understanding Predictive Maintenance (PDM)
How AI and Data Analytics Enable Predictive Maintenance
Key Components of AI-Driven Predictive Maintenance
Using artificial intelligence-driven predictive maintenance involves a few key components:
Data Collection and Processing
PDM begins with IoT sensors and devices continually monitoring machinery and sending data to central systems. Continuously gathering data on equipment conditions, these sensors detect temperature, pressure, and vibration. Often used for storage and processing this data are cloud-based solutions, which guarantee scalability and simple access for analysis.
Machine Learning Models
Artificial intelligence uses machine learning (ML) algorithms to forecast equipment failure. These algorithms are taught utilizing past data to identify particular trends pointing to possible problems. Anomaly detection models, for example, can highlight anomalies in machine performance or highlighting discrepancies pointing to wear or failure. Especially when tracking equipment with complicated operational patterns, neural networks, and time-series analysis are also somewhat frequently utilized.
Data Analysis and Decision-Making
AI’s true potential is in enabling the analysis to be taken action after the data is analyzed. It produces predictive insights and alarms, therefore enabling maintenance teams to respond proactively. For instance, a maintenance crew can act before the machine fails if artificial intelligence identifies an increase in vibration levels indicating possible bearing wear. Such realizations help flexible, just-in-time treatments instead of depending on scheduled maintenance cycles.
Benefits for Industries like Manufacturing
Predictive maintenance powered by artificial intelligence offers significant advantages in sectors where operational efficiency is a top priority:
- Reduced Downtime: PDM helps reduce unplanned breakdowns by estimating when equipment is most likely to fail. In an industry, where unscheduled downtime may stop lines of production and affect delivery dates, this is vital.
- Cost Savings: Reducing unneeded preventative maintenance schedules and lowering unscheduled repairs helps to minimize maintenance expenses. PDM helps businesses save costs by letting them concentrate resources where they are required. For instance, Airbus said that using predictive maintenance solutions powered by artificial intelligence resulted in a 20% drop in maintenance expenses.
- Extended Equipment Lifespan: AI’s exact observations of equipment condition enable prompt repair based on which wear and tear is prevented from developing into irreversible harm. This preventative maintenance helps machines last longer over time, therefore postponing the need for expensive replacements.
Challenges and Considerations
Data Quality and Quantity: High-quality data is mostly relied upon by artificial intelligence models to provide reliable forecasts. Low-quality or inconsistent data might produce inaccurate forecasts, therefore compromising the efficacy of the system.
Implementation Costs: Setting up AI-powered PDM solutions calls for IoT infrastructure, data storage, and qualified people investments. Though the long-term benefits are significant, smaller businesses may find the early expenses exorbitant.
Skills Gap: AAI-driven PDM depends on knowledgeable staff to manage, understand, and polish data insights. Businesses might have to make training investments, recruit experts, or explore outsourcing predictive AI projects to providers with established expertise to make good use of the data AI offers.
Conclusion
Predictive maintenance will get even more advanced as artificial intelligence develops and provides quicker, more accurate insights. Organizations that lack in-house AI expertise can consider outsourcing predictive AI development and implementation to specialized partners to accelerate adoption. Looking ahead, artificial intelligence’s influence on maintenance and asset management will only become more apparent; maybe a day when operations run at perfect efficiency, maintenance is completely predictive, and equipment failure is a thing of the past.
If you’re ready to embark on this journey and need expert guidance, subscribe to our newsletter for more tips and insights, or contact us at Offsoar to learn how we can help you build a scalable data analytics pipeline that drives business success. Let’s work together to turn data into actionable insights and create a brighter future for your organization.
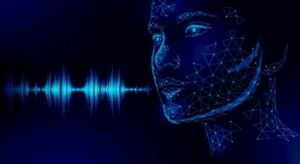
How LLMs Are Revolutionizing Text Mining and Data Extraction from Unstructured Data
Leveraging LLMs for Advanced Text Mining and Data Extraction from Unstructured Data Since digital transformation is growing exponentially, businesses generate huge amounts of unstructured data from sources like emails, PDFs,
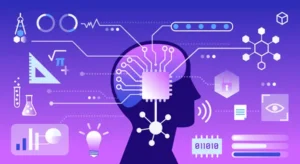
How Businesses Use LLMs for Competitive Intelligence to Stay Ahead of the Curve
How Businesses Use LLM’s for Data-Driven Competitive Intelligence to stay ahead of the curve Competitive intelligence (CI) is essential for keeping a competitive edge in today’s fast-paced business world. Businesses
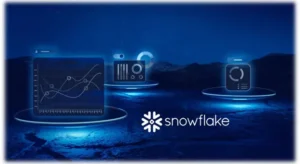
Maximizing Cost-Efficient Performance: Best Practices for Scaling Data Warehouses in Snowflake
Maximizing Cost-Efficient Performance: Best Practices for Scaling Data Warehouses in Snowflake Organizations rely on comprehensive data warehouse solutions to manage substantial volumes of data while ensuring efficiency and scalability. Snowflake,
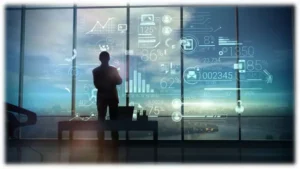
Comprehensive Guide to Implementing Effective Data Governance in Snowflake
Mastering Data Governance with Snowflake: A Comprehensive Guide Data governance is a systematic way to manage, organize, and control data assets inside an organization. This includes developing norms and policies
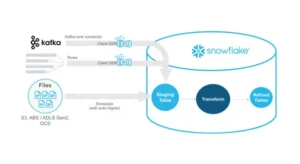
Efficiently Managing Dynamic Tables in Snowflake for Real-Time Data and Low-Latency Analytics
Managing Dynamic Tables in Snowflake: Handling Real-Time Data Updates and Low-Latency Analytics In this data-driven environment, businesses aim to use the potential of real-time information. Snowflake’s dynamic tables stand out
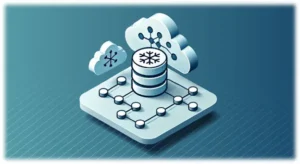
Mastering Data Lineage and Traceability in Snowflake for Better Compliance and Data Quality
Mastering Data Lineage and Traceability in Snowflake for Better Compliance and Data Quality In data-driven businesses, comprehending the source, flow, and alterations of data is essential. Data lineage is essential